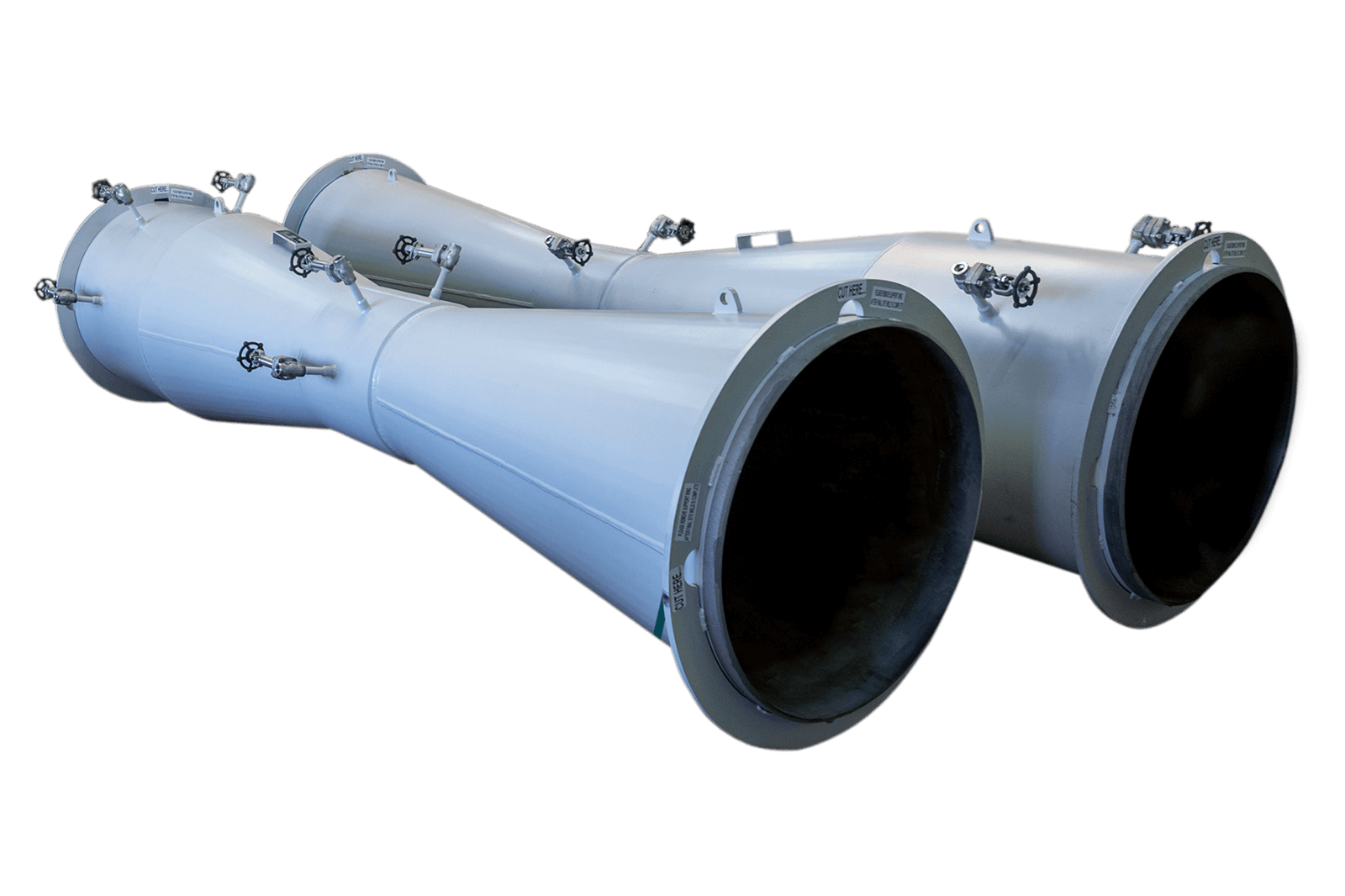
Venturi flow meters play a crucial role in industrial applications, offering precise and reliable measurements of fluid flow rates.
Understanding their significance and optimising their performance is essential for ensuring accurate process control and efficiency in various industrial processes.
Importance Of Accurate Flow Measurement
Accurate gas flow measurement is vital in industries for several reasons. Precise measurements ensure the efficient operation of various processes, including chemical manufacturing, power generation, and HVAC systems.
In these industries, even slight deviations in flow rates can lead to inefficiencies, reduced product quality, or equipment damage.
Accurate flow measurement is crucial for safety considerations. In industries handling flammable or hazardous gases, improper flow rates can pose significant safety risks, including fire hazards or toxic gas exposure.
Moreover, precise flow measurement is essential for compliance with regulatory requirements and industry standards. Many industries are subject to regulations governing emissions, product quality, and process efficiency. Accurate flow meters ensure compliance with these standards.
Additionally, accurate gas flow measurement facilitates effective process control and optimisation. By monitoring and adjusting flow rates in real time, industries can optimise production processes
How Venturi Flow Meters Work
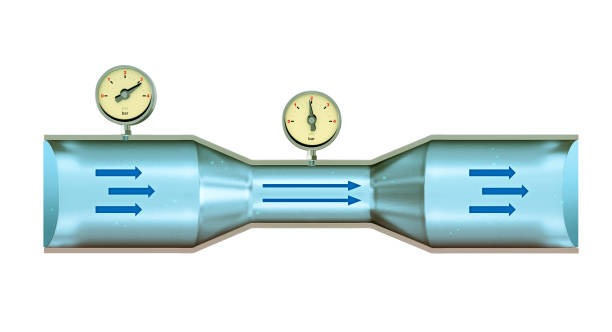
Venturi meters operate on the principle of Bernoulli’s equation, using the Venturi effect to accurately measure flow rates. As fluid flows through the venturi tube and the flow nozzle, its velocity increases, leading to a corresponding decrease in pressure.
The mass flow rate can be determined with high accuracy by measuring the differential pressure between the throat section and the inlet.
Advantages Of Using Venturi Meters
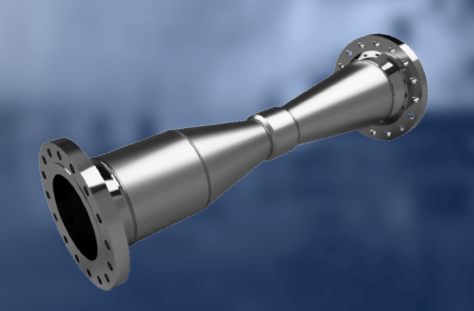
Venturi meters offer several advantages that make them the preferred choice for flow measurement in various industrial applications. These advantages include:
- Accuracy: Venturi tubes provide precise and reliable flow measurements across a wide range of flow rates and fluid types. Their design minimises pressure loss, resulting in accurate readings even in challenging operating conditions.
- Low-pressure drop: Compared to other flow measurement devices like orifice plates, Venturi meters produce minimal pressure drop, reducing energy consumption and operating costs.
- Wide turndown ratio: A Venturi meter maintains accuracy over a broad range of flow rates, allowing for flexibility in applications where flow rates may vary significantly.
- Minimal maintenance requirements: Venturi meters have simple and robust designs, requiring little to no maintenance once installed properly. This reduces downtime and maintenance costs associated with calibration and servicing.
- Versatility: Venturi meters can be used with various fluids, including liquids, gases, and steam, making them suitable for a wide range of industrial processes and applications.
- Long-term reliability: With proper installation and periodic calibration, Venturi meters can provide accurate flow measurements for extended periods, ensuring reliable performance and operational efficiency.
Factors Impacting The Accuracy Of Venturi Meters
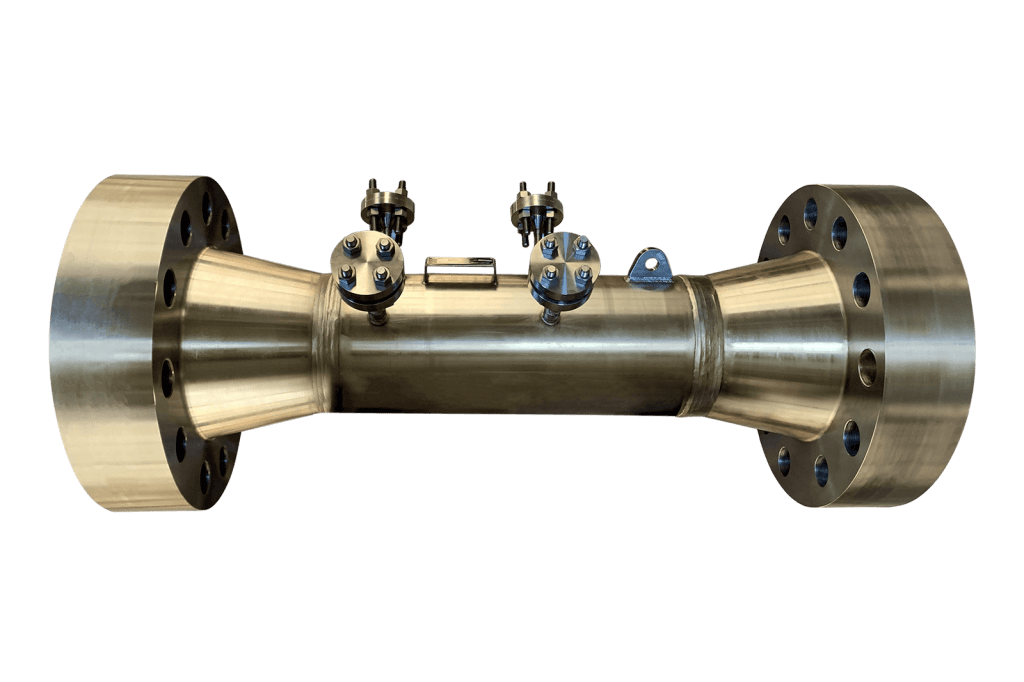
Achieving optimal performance from a venturi flow meter requires a comprehensive understanding of the various factors that can influence their accuracy:
- Fluid properties: Variations in fluid density, viscosity, and composition can influence meter accuracy, highlighting the need for comprehensive fluid characterisation.
- Flow profile: Non-uniform flow profiles, caused by obstacles or bends in the piping system, can introduce inaccuracies in meter readings, emphasising the importance of proper piping design.
- Installation conditions: Correct meter installation, including appropriate straight pipe lengths and orientation, is crucial for minimising flow disturbances and ensuring accurate measurements.
- Meter design: Parameters such as throat diameter, convergence angle, and length can affect meter accuracy, underscoring the importance of selecting the right meter design for specific applications.
Common Challenges Of Flow Velocity In Industrial Settings
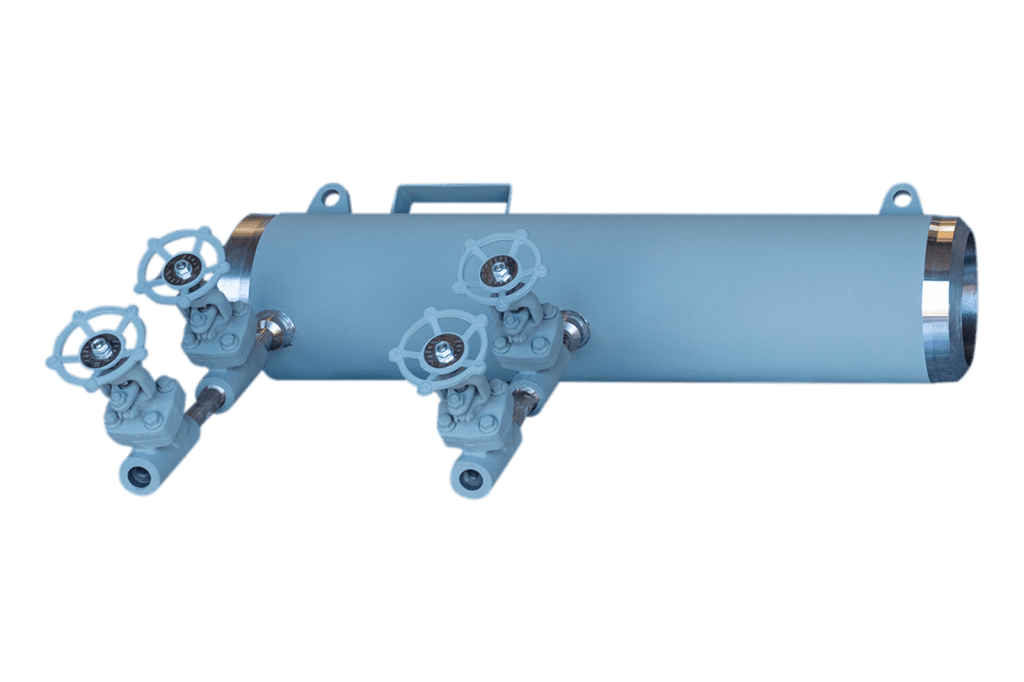
Numerous challenges can impede the accurate assessment of flow velocity, impacting the reliability of industrial processes:
Harsh operating conditions
Extreme temperatures, pressures, and corrosive environments common in industrial settings can impact meter performance, necessitating robust and durable meter construction materials.
Flow disturbances
Obstacles, bends, and changes in pipe diameter can disrupt flow patterns, leading to inaccuracies in meter readings and highlighting the need for proper flow conditioning measures.
Maintenance requirements
Regular calibration, inspection, and cleaning are essential for ensuring optimal meter performance and minimising the risk of measurement errors over time.
Strategies For Optimising Venturi Meter Performance
Enhancing the efficiency and accuracy of Venturi meters in industrial applications necessitates the implementation of strategic optimisation techniques:
- Proper installation: Following guidelines for correct meter installation minimises flow disturbances and ensures accurate readings.
- Calibration and validation: Periodic calibration and validation procedures help maintain meter accuracy and reliability over time.
- Flow conditioning: Utilising flow conditioning devices improves flow profiles and enhances meter accuracy, particularly in applications with turbulent flow conditions.
- Material selection: Choosing robust and corrosion-resistant materials for meter construction ensures longevity and performance in harsh industrial environments.
- Monitoring and diagnostics: Implementing real-time monitoring and diagnostic tools enables prompt detection and resolution of meter issues, minimising downtime and optimising process efficiency.
In Summary
Maximising the performance of Venturi meters in industrial applications requires a thorough understanding of their operation, careful consideration of influencing factors, and implementation of optimisation strategies.
By adhering to the best installation, maintenance, and monitoring practices, industrial operators can ensure accurate and reliable flow measurements essential for efficient process control.
Explore Our Range Of Venturi Meters
Discover our comprehensive selection of McMenon Venturi meters tailored to meet the diverse needs of industrial applications. Contact us today for personalised assistance and quotes, and take the first step towards optimising your industrial processes.