Over the years the industry has developed several approaches to measure and control flow in process applications. Some examples that have successfully emerged over the years are magnetic flow meters, Coriolis flow meters, vortex meters, thermal dispersion flow meters and a wide array of differential producing primary elements.
One of the oldest methods of measuring flow is installing a differential producing device in the line to create the pressure drop. And with this method the orifice plate is still commonly used. Other differential producing devices are wedge meters, pitot meters, VENTURI meters, cone type meters, and others.
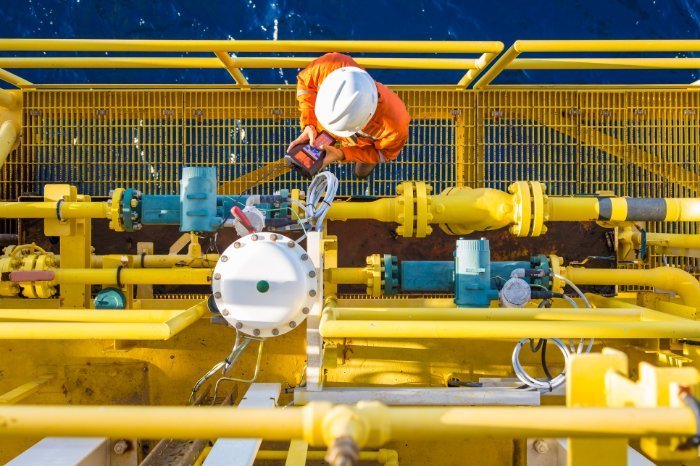
One of the oldest methods of measuring flow is installing a differential producing device in the line to create the pressure drop. And with this method the orifice plate is still commonly used. Other differential producing devices are wedge meters, pitot meters, VENTURI meters, cone type meters, and others.
Many knowledgeable industry professionals will tell us that there is no one size fits all approach to tackling flow measurement. The process itself, plus economics and performance expectations, all go into analyzing the best approach to employ.
- When utilizing the DP method for accurately measuring flow the user must know the following.
- The specific gravity or density of the fluid being measured
- Chemical compatibility of the fluid to materials being employed
- The minimum and maximum flow rates expected
- Static pressure and temperature of the fluid (particularly in gas measurement applications)
- The pipe inside diameter
- The parameters of the primary element (In the case of the orifice plate, the bore dimension and bore location within the plate)
- The user must analyze the flow profile within the pipe to ensure that there is enough fully developed turbulent flow to extract an accurate measurement (Reynolds number calculations come into play and piping conditions in the process should be analyzed upstream and downstream)
- How much differential pressure does the user want to create? Does the created DP properly match the flow computer or transmitter? How much pressure drop is acceptable in the flow stream?
So, where do the valve products come in and why are they so important? We can think of the valves as service valves between the primary meter and the measuring instrument (DP transmitter or flow computer). The valves simply allow the user to block in, calibrate or verify calibration, replace instruments and vent entrapped pressure without shutting the critical process down.
Stabilized Connectors, with or without the integral block valve:
- Mounted onto the orifice flange or the orifice fitting
- Sometimes referred to as a “Root Valve” or primary isolation valve
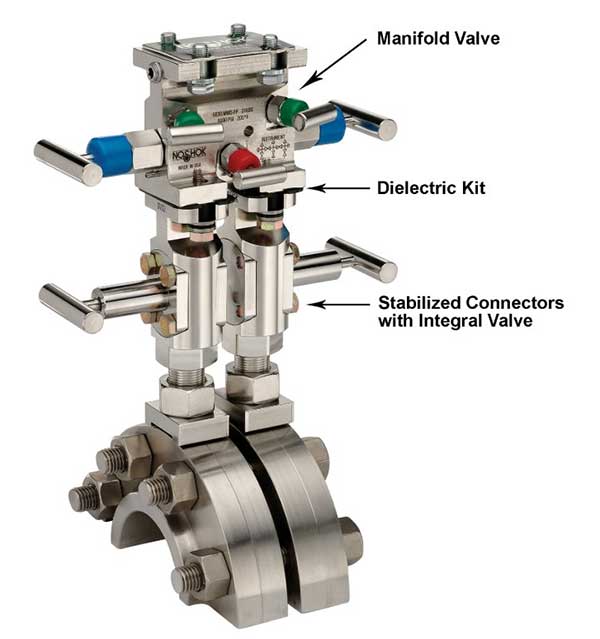
Dielectric Kits are often mounted between the stabilized connector and the manifold valve:
- The purpose of the dielectric kit is to insulate any EMF or static electricity from migrating from the process piping to the transmitter or flow computer electronic circuit board.
The Manifold Valve
- Can be purchased in several configurations, soft seat, hard seat, 2-valve types, 3-valve types or 5-valve types
- Variety of materials can be supplied but stainless steel and carbon steel are most common
- Standard bore or large bore design for custody transfer applications
- The manifold valve offers high and low pressure isolation (pressure upstream and downstream of the differential producing element)
- The manifold valve offers the ability to equalize the DP pressure to the transmitter or flow computer. This is important when the user wants to see zero differential to verify the “zero signal output” during a calibration check (Single valve for equalizing, or double redundant equalizing valves to conform to industry specifications with custody transfer)
- The manifold valve can offer a dedicated vent valve to vent entrapped pressure during service operations
NOSHOK’s Direct Connect Assembly shown above provides an installation that keeps the meter close to the orifice taps for accurate flow measurements.
There are a wide array of applications where flow measurement and control is essential:
- Liquids or gases
- Petrochemical and refining
- Gas processing facilities
- Power generation facilities
- Utilities
- Water and Waste Water facilities
- Pipeline applications
- Custody transfer metering stations
- Plus many other applications not noted
In conclusion, valves play an extremely important role in allowing the user to safely operate and service instrumentation in their processes. The goal of every application and every good supplier is to work in a collaborative manner to achieve the following:
- Safety
- Protection of valuable assets
- Reduce down time during maintenance operations
- Lower maintenance cost through efficiency
- Provide accuracy in the measurement process
For further information you can also contact Dave Grey dave.g@ams-ic.com.au