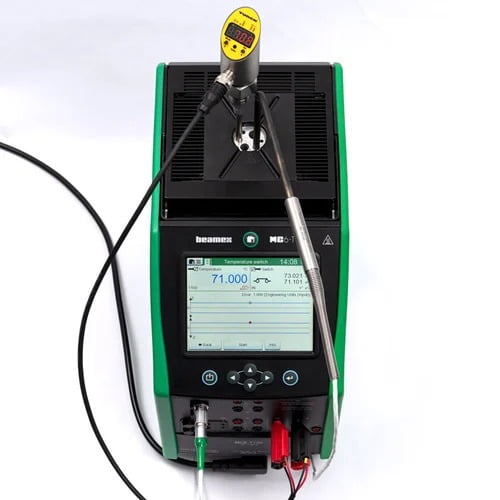
In today’s highly automated and technologically advanced industrial landscape, precise temperature measurement is essential for ensuring product quality, operational safety, and regulatory compliance.
Temperature sensors play a pivotal role in this endeavour, as they provide the data needed to monitor, control, and optimise various industrial processes.
This guide aims to equip you with the essential knowledge and insights required to navigate the intricacies of temperature sensor calibration within industrial settings.
Significance of Precise Temperature Measurements
When you calibrate temperature sensors, slight temperature variations can lead to defects in manufactured products, catastrophic failures in oil and gas refineries, inefficient energy consumption in HVAC systems, or food safety hazards.
Accurate temperature measurements are the foundation upon which these industries rely to function effectively and safely.
Importance of Temperature Sensors in Industrial Processes
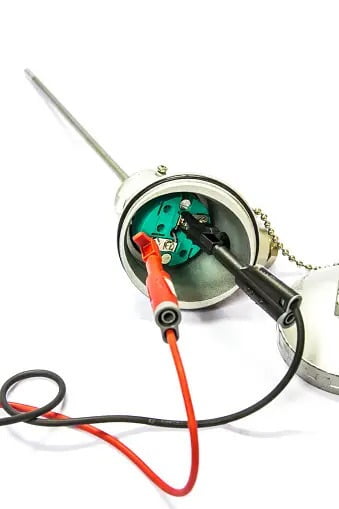
Temperature sensors are integral components of industrial processes, silently carrying out the crucial task of monitoring and controlling temperature variations.
These devices are essential for maintaining the delicate balance of temperature required for different operations.
Temperature sensors provide precise measurements that impact product quality, safety, and energy efficiency across industries, making them indispensable tools in the modern industrial landscape.
Overview and Working Principles of Temperature Sensors
Before diving into the intricacies of calibration, it’s crucial to understand the different types of temperature sensors and their working principles.
Temperature sensors come in various forms, but three common types include Resistance Temperature Detectors (RTDs), Thermocouples, and Infrared Sensors.
Each type operates on a unique principle, allowing them to measure temperature accurately within their respective temperature ranges.
Common Challenges in Temperature Sensor Calibration
While the calibration process might seem straightforward, several challenges can arise, particularly in demanding industrial settings.
- Extreme Temperature Calibration: In industries, extreme temperatures are the norm. Calibrating temperature sensors in such environments requires specialised equipment and expertise to ensure temperature range accuracy.
- Ensuring an Unbroken Chain of Calibration: Maintaining the traceability and sensor accuracy of calibration standards is crucial. Any break in the chain can lead to inaccuracies in subsequent calibrations, potentially compromising the entire measurement process.
- Comparing Readings Across Different Sensors: When multiple sensors are involved in a process, ensuring that they all provide consistent readings is essential. Calibration helps harmonise these readings, minimising discrepancies.
Factors Influencing Temperature Calibration
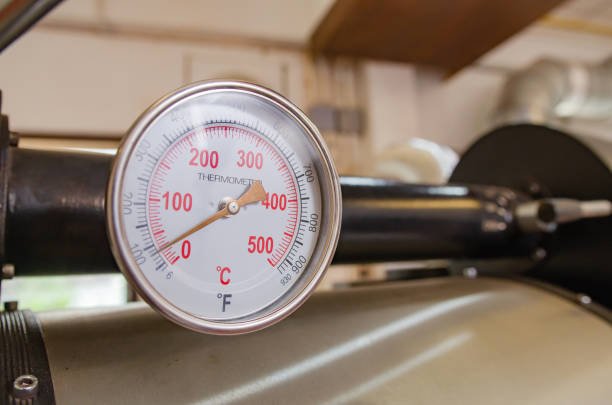
Several factors influence the calibration process, and understanding them is essential for achieving precise temperature readings. Here are some key factors:
- Sensor Type: Different sensor types have varying calibration requirements due to their inherent characteristics. Understanding the sensor type is crucial for selecting the appropriate calibration method and equipment.
- Environmental Conditions: Ambient temperature, humidity, and pressure can affect sensor performance. Calibrations should account for the environmental conditions in which the sensor will operate to ensure accurate measurements.
- Calibration Equipment: The quality and accuracy of the calibration equipment, such as a temperature probe, dry-block calibrators, and reference standards, significantly impact the calibration process. Regular maintenance and calibration of these tools are essential.
- Calibration Intervals: Establishing a calibration schedule based on the sensor’s usage and manufacturer’s recommendations is vital. Frequent calibrations may be necessary for sensors operating in harsh conditions, while less critical applications may require less frequent calibrations.
- Stability and Aging: Over time, sensors may drift or experience aging effects, affecting their accuracy. Monitoring sensor stability and accounting for any drift in calibration processes is crucial for long-term reliability.
- Data Analysis and Correction: Post-calibration data analysis may reveal systematic errors that require correction. Applying correction factors or adjustments based on calibration results can improve measurement accuracy.
Temperature Sensor Calibration in Different Industries
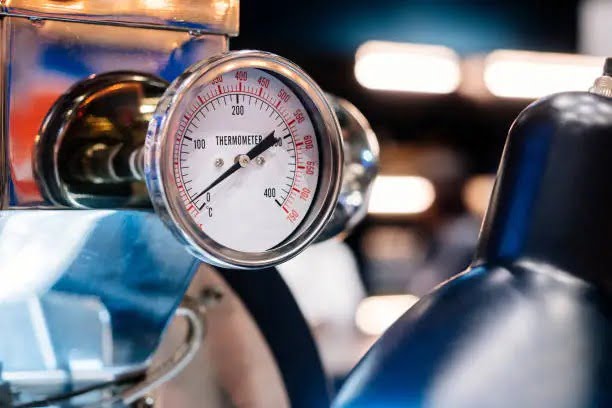
Manufacturing Industry
In manufacturing, precise temperature measurements are critical for processes like semiconductor fabrication and pharmaceutical production. Calibration guarantees product quality and consistency.
Oil and Gas Industry
The oil and gas industry relies on temperature sensors to monitor extreme conditions in pipelines and refineries. Accurate measurements are crucial for safety and operational efficiency.
HVAC Industry
Heating, ventilation, and air conditioning systems are essential for maintaining comfortable indoor environments. Temperature sensor calibration ensures energy-efficient operation and occupant comfort.
Food and Beverage Industry
Temperature plays a pivotal role in food safety and quality. Calibration of temperature sensors in food and beverage production ensures compliance with regulations and delivers safe products.
Tips for Precise Temperature Calibration
Calibrating temperature sensors is a critical process to ensure accurate and reliable measurements in various applications. Here are some professional tips to achieve precise temperature sensor calibration:
- Select the Right Calibration Method: Choose the appropriate calibration method based on the sensor type and the required accuracy level. Common methods include comparison, simulation, and interpolation.
- Understand Measurement Uncertainty: Calculate and consider measurement uncertainty to understand the potential errors associated with calibration. This helps in determining the overall reliability of temperature measurements.
- Calibrate at Multiple Points: Perform calibration at multiple temperature points within the sensor’s operational range. This provides a more thorough assessment of the sensor’s performance.
- Evaluate Sensor Stability: Monitor the stability of temperature sensors over time. Frequent calibrations may be necessary if sensors exhibit drift or instability.
- Adhere to Regulatory Requirements: In regulated industries, compliance with specific calibration standards and requirements is essential. Ensure that your calibration processes meet international standards.
- Perform Repeatability Checks: After you calibrate a temperature sensor, conduct repeatability checks to verify that the sensor provides consistent results when measuring the same temperature multiple times.
In Summary
By understanding the importance of calibration and its role in ensuring reliable temperature measurements, industries can navigate the complexities of temperature-dependent processes with confidence.
Calibration is the bedrock upon which industries rely to maintain quality, safety, and efficiency in their processes.
For all your calibration and instrumentation needs, visit our product page and get in touch with our experts. Precision and reliability are just a click away.