
In today’s data-driven industrial world, precision isn’t just a perk — it’s non-negotiable. And nowhere is that more critical than when managing one of our most vital and volatile resources: water.
So, what is the function of water level sensor technology?
Put simply, water level sensors play a pivotal role in measuring, monitoring, and managing the water level within tanks, pipelines, reservoirs, and more — triggering actions based on fluctuations. Whether it’s keeping a food production line running smoothly or preventing overflow in a mining slurry tank, these silent workhorses ensure everything flows exactly as it should.
Let’s unpack how they keep operations running safely and efficiently — and why companies across mining, agriculture, manufacturing, and beyond rely on high-quality instrumentation from AMS.
The Backbone of Industrial Efficiency: Why Water Level Sensors Matter
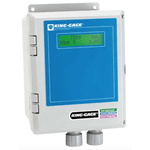
Water level sensors are more than just gadgets. They’re the eyes and ears of your system, providing real-time water level data that can make or break productivity.
- In industrial processes, misjudging the liquid level in a tank can cause overflow, contamination, or system failure.
- For irrigation systems, smart water level sensing avoids waste and ensures crops get exactly what they need.
- At wastewater treatment plants, water level sensors play a central role in ensuring environmental compliance and public safety.
And in every one of those cases, the consequences of inaccurate readings range from costly downtime to catastrophic damage.
How Do Water Level Sensors Work?
At the heart of these systems is a sensor that measures the distance between the sensor head and the liquid surface — often using sound wave, air pressure, or hydrostatic pressure.
Here’s how various technologies work:
- Ultrasonic level sensors send an ultrasonic pulse that reflects off the water surface, calculating distance by timing the echo.
- A diaphragm liquid level sensor uses the internal pressure created by rising liquid levels to trigger a micro switch inside the device.
- A float switch or float level sensor physically rises and falls with the liquid level, activating a mechanical switch when a set point is reached.
- Pressure-based options like a pressure transducer or pressure level sensors detect changes in pressure exerted by the water column and convert it into an electrical signal.
Each sensor converts these physical interactions into data your control systems can act on — all in real time.
Common Applications Across Industries
Water level sensors aren’t just useful — they’re essential in dozens of sectors:
- Mining & mineral processing: Monitoring slurry tanks, sediment ponds, and dust suppression systems.
- Food & beverage: Managing sterile water flow and wastewater during high-volume production.
- Agriculture: Smart water allocation in irrigation systems and water tanks for livestock and crops.
- Municipal waterworks: Regulating reservoirs, storm drains, and commercial swimming pools.
- Oil & gas: Detecting volume shifts in oil tanks and fuel systems with a fuel level indicator.
- Urban infrastructure: Rainwater collection and sewer overflow prevention during storms.
Across all of them, accurate level measurement means the difference between smooth sailing and disaster.
Types of Water Level Sensors: Choosing the Right Tool for the Job
Not all level sensors are created equal — here’s a breakdown of the major players and when to use them:
- Float switches / float level sensors / float sensors: Simple, mechanical, and great for basic on/off control in tanks or pits.
- Ultrasonic level sensors / ultrasonic liquid level sensor / ultrasonic water level sensor: Non-contact, great for corrosive or hazardous liquids.
- Diaphragm liquid level sensor: Ideal for measuring air pressure changes without exposing electronics to the liquid.
- Tuning fork level sensor / tuning fork level gauge: Perfect for point level detection in foamy or turbulent conditions.
- Pressure transducer or pressure sensors: Ideal for high-accuracy readings in pressurised systems.
- Fork level sensor: Suited for binary detection in clean or viscous liquids.
- Continuous level sensors: Used in continuous level measurement scenarios for full-range readings.
- Ultrasonic sensors and infrared light devices: Ideal where non-contact sensing and optical detection is needed.
Each sensor type is tailored for specific environments, making sensor selection crucial — the wrong choice can lead to sensor drops, faulty readings, or even equipment failure.
Technology Deep Dive: How Sensors Work Together
A well-designed system doesn’t rely on a same sensor across all use cases — it layers technologies:
- Digital level gauge controlled systems combine multiple input types for real-time automation.
- The sensor head emits an ultrasonic pulse, which interacts with the liquid surface and reflects back to the ultrasonic transducer.
- Changes in ambient light or low power consumption requirements are addressed using infrared and energy-efficient configurations.
- Detection tubes, micro switch setups, and internal power supply redundancies ensure continuous monitoring.
The goal? Manage water flow, react instantly, and maintain precise measurements with minimal operator involvement.
AMS: Delivering Reliable, Calibrated Sensor Systems
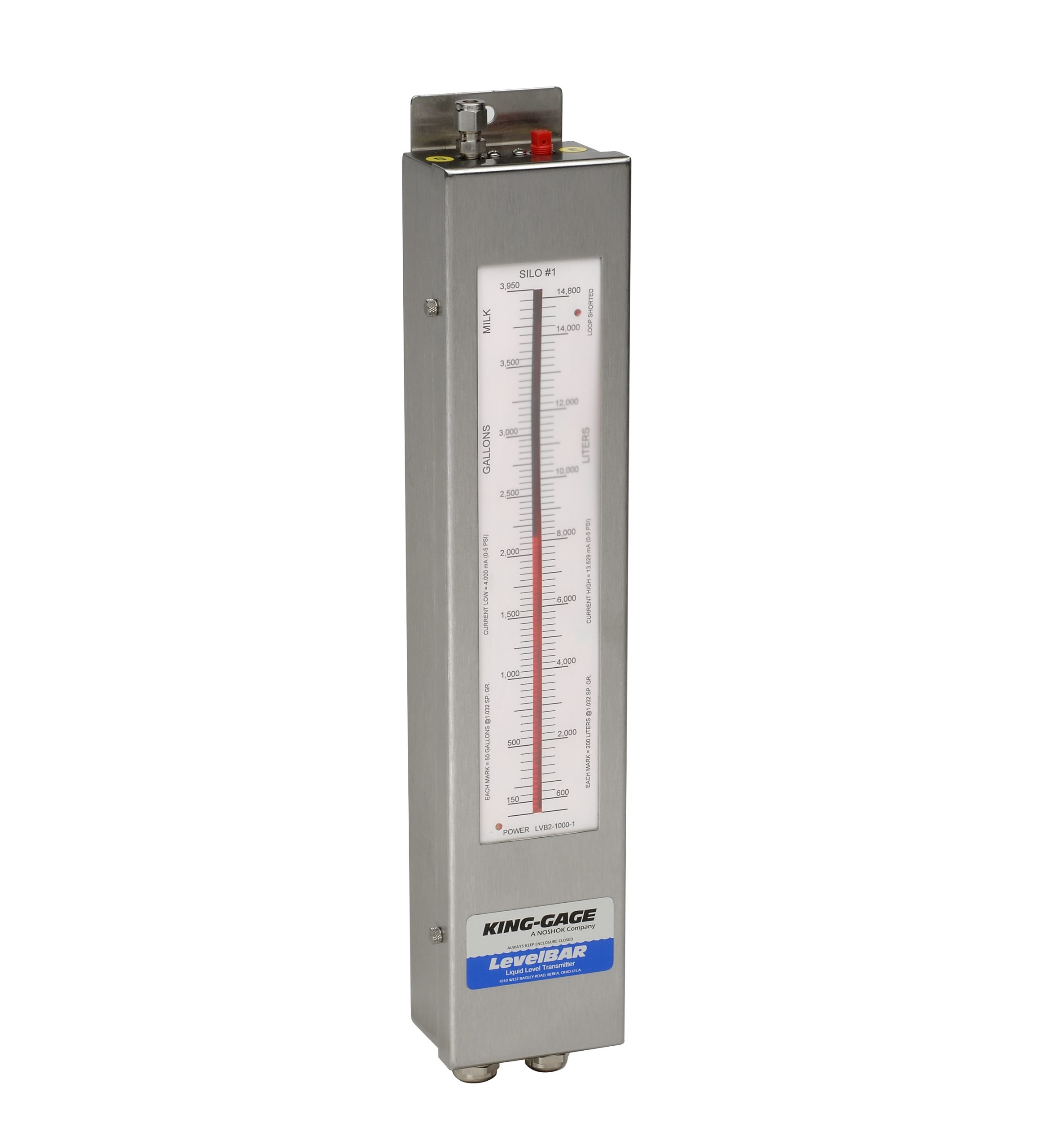
At AMS, we understand that liquid level isn’t just a number — it’s a critical control point in your operation.
That’s why we provide:
- Top-tier instrumentation tailored to your industry and application
- Fully calibrated liquid level monitoring systems ready for deployment
- Expert recommendations on the best level sensor for your specific process
- End-to-end service — from installation to maintenance to emergency support
Whether you’re overseeing industrial tanks, water resources, or delicate process fluids, AMS has the sensor solution built for accuracy, durability, and trust.
Don’t Let Water Waste or System Failures Drain Your Profits
If you’re still relying on outdated methods — or worse, cheap sensors that fail when it counts — you’re playing a dangerous game with your operations.
High-quality water level sensors don’t just prevent problems. They maximise efficiency, reduce costs, and protect your assets — from liquid level drops to catastrophic overflows.
AMS works with Australia’s top industries to provide calibrated, industrial-grade instrumentation that’s ready for the toughest environments. Our water level sensor solutions aren’t just accurate — they’re battle-tested in the real world.
Want to talk to someone who actually knows how to measure the water level properly?
Visit our Contact Us page today — and speak with an instrumentation expert who’ll guide you to the right solution for your operation.